Types of Underwater Welding
- Jason Harwood
- Mar 25
- 3 min read
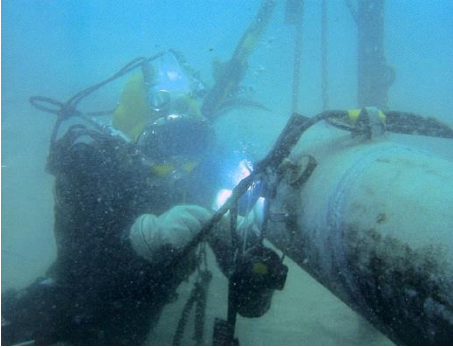
Ever wondered what underwater welders do?
Underwater welding is a critical skill in the marine industry, allowing welders to repair and maintain ships, pipelines, oil rigs, and other submerged structures. However, not all underwater welding types are the same. Depending on the job, welders use wet or dry welding, each with its techniques, advantages, and risks.
So, what are the types of underwater welding, and how do they work? This guide breaks it down, from the most common methods to the equipment used and where they’re applied.
The Two Main Types of Underwater Welding
There are two primary underwater welding types—wet welding and dry welding. The choice depends on factors like project depth, safety, and the quality of the weld needed.
Wet Welding: Welding Directly in Water
Wet welding happens underwater, meaning the welder is fully submerged while working. This method is used for quick repairs and emergency fixes where setting up a dry workspace isn’t practical.
The most common technique used for wet welding is Shielded Metal Arc Welding (SMAW), also called stick welding. This process uses waterproof electrodes that generate gas bubbles around the weld to shield it from water. However, because of rapid cooling and limited visibility, wet welds are more prone to defects and may not be as strong as dry welds.
Pros and Cons of Wet Welding
Pros
Lower cost: No need for expensive equipment like hyperbaric chambers
Faster setup: Ideal for emergency repairs
Easier access: This can be done in hard-to-reach underwater locations
Cons
Lower weld quality: Water cools the weld too quickly, increasing the risk of cracks
Higher risks: Welders must be cautious of electric shock hazards
Poor visibility: Working in open water means reduced control over the welding process
Dry Welding: Creating a Controlled Environment
Unlike wet welding, dry welding (hyperbaric welding) is performed inside a sealed chamber filled with gas. This chamber is placed over the weld site, keeping water out and allowing for higher-quality, more controlled welds.
Because the welder isn’t directly exposed to water, dry welding is the preferred method for high-precision and long-lasting repairs. It’s widely used in industries such as offshore oil and gas, shipbuilding, and marine construction.
Types of Dry Welding Chambers
There are several types of dry welding setups, each designed for different depths and project requirements:
Hyperbaric Welding Chambers: Large sealed chambers where welders can work in a dry, pressurised environment
Dry Spot Welding: Small watertight enclosures are placed over the weld site to create a dry workspace
Cofferdams: Temporary enclosures are used to drain water from a section of a structure, allowing welding to be done in the air
Pros and Cons of Dry Welding
Pros
Higher weld quality: More precise and durable than wet welding
Safer for the welder: No direct exposure to water or electrical hazards
Better visibility: A dry, controlled environment allows for more accurate work
Cons
Expensive setup: Requires special equipment like hyperbaric chambers
Time-consuming: Takes longer to set up than wet welding
Limited mobility: Chambers may not fit all welding locations
Equipment For Underwater Welding
Whether using wet or dry welding, underwater welders need specialised equipment to ensure safety and efficiency. So, what equipment do you need for underwater welding?
Diving helmets: Provide oxygen and allow communication
Waterproof welding electrodes: Used in wet welding to create a stable arc
Hyperbaric welding chambers: Used for dry welding to keep the work area free from water
Breathing gas mixtures: For deep dives, welders use Heliox (helium and oxygen) to prevent health issues
Having the right gear is crucial for underwater welders to do their job safely.
How Deep Do They Go?
How deep do underwater welders go? The depth an underwater welder works depends on the welding method and project requirements.
Wet welding is typically done at depths of up to 130 feet (40 metres)
Dry welding can be performed as deep as 1,000 feet (300 metres) using saturation diving techniques
Deeper work requires advanced equipment and strict safety measures to handle high-pressure environments.
Do You Need Professional Underwater Welding Services?
All types of underwater welding are vital in maintaining marine infrastructure, but it requires the right skills, equipment, and experience to be done safely and effectively. Working with trained professionals is key, whether it’s ship repairs, oil rig maintenance, or underwater construction.
Are you looking for expert underwater welding services? Trust industry professionals, like Harcan Marine, who specialise in high-quality, safe, and efficient welding solutions.
Comentários